Wiped Film Evaporator Systems
Systems
Wiped Film Evaporator Systems: Efficient Solutions for Heat-Sensitive, Fouling, and High-Viscosity Applications
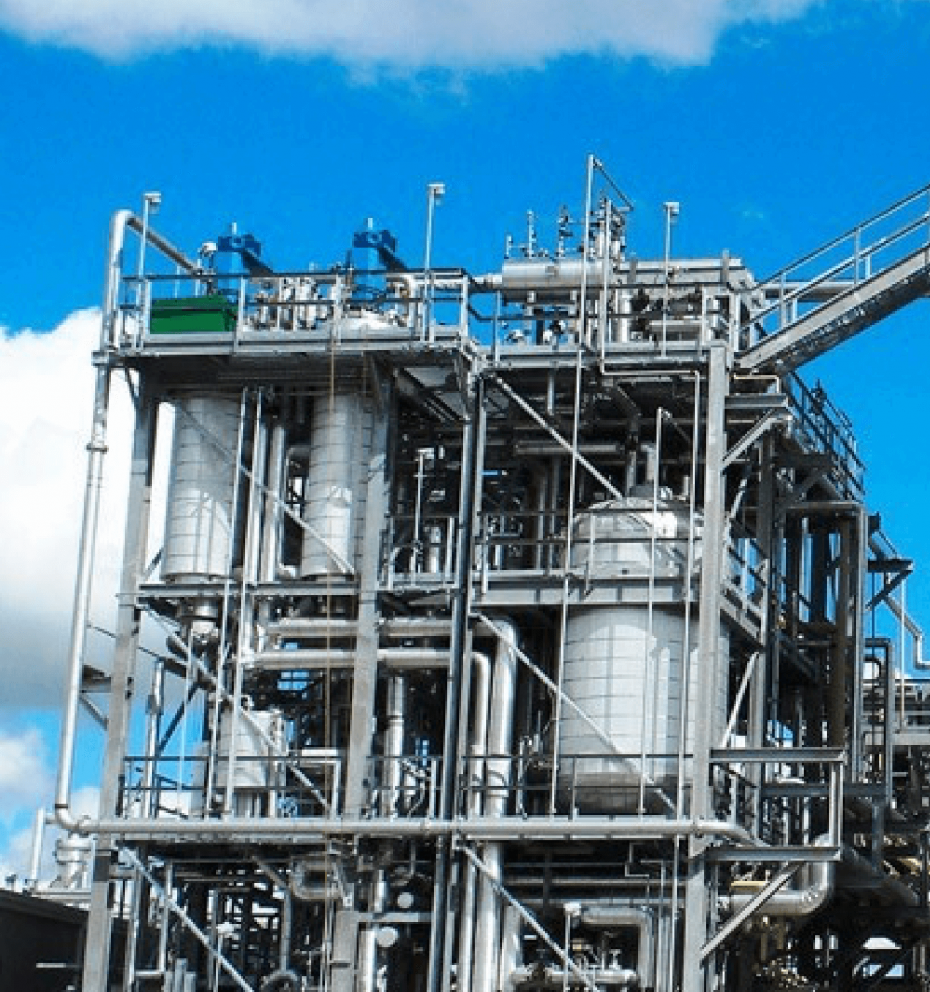
Introduction to Our Wiped Film Evaporator Systems Expertise
Engineers at GMM Pfaudler Systems are responsible for the design and delivery of EQUILLOY brand Wiped Film Evaporators (WFEs) within a comprehensive system. Every aspect of the system design will be considered, including the process requirements for capacity, purity and yield, the utility requirements, and the complete integration of the vacuum system design, to guarantee optimal system performance.
We are dedicated to delivering a complete WFE System that is highly effective, reliable and will help you attain peak performance from your process.
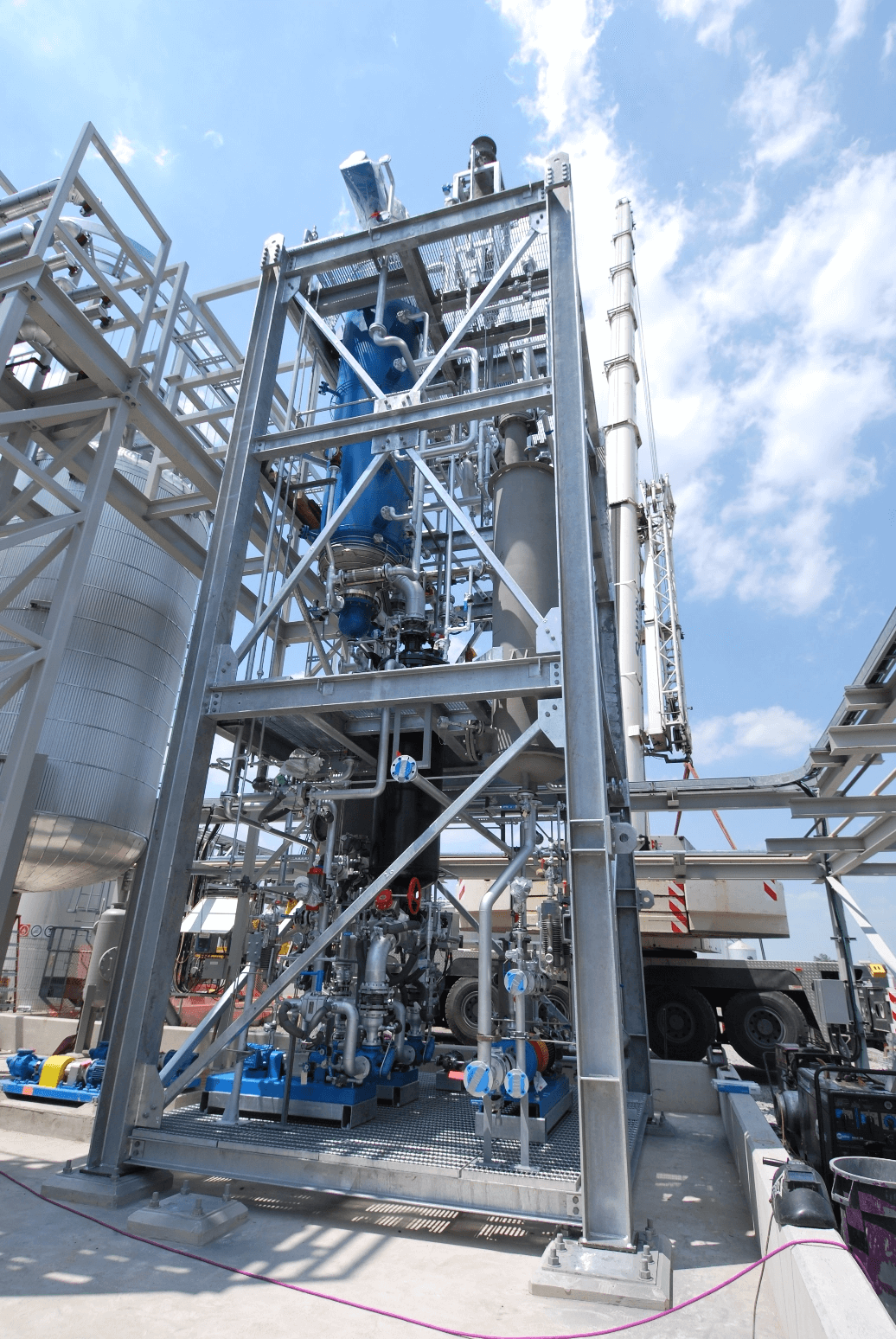
What Defines a System in Wiped Film Evaporator Technology
- Process engineering
- Project engineering
- Project management
- 3D CAD design of module
- Feed tank, pump and pre-heater
- Degassers
- Residue tank and pump
- Distillate tank and pump
- Product cooler
- Vacuum system
- Process and utility piping
- Instrumentation
- PLC control system
- Structural steel support skid
- Thermal fluid heating system
Critical Process Design for Wiped Film Evaporator Systems
There are many aspects to a complete Wiped Film Evaporator Process System, including preheating, degassing, devolatilization, vacuum, utilities, and product and waste handling. Our process engineers design all critical processes surrounding the Wiped Film Evaporator, to ensure that the entire system is completely integrated. This includes:
Feed flow control
Preheating, while preventing degradation and fouling, especially crucial for heat sensitive materials.
Degassing to minimize load on the vacuum system.
Wiped Film Evaporator (WFE) design for optimum separation, yield, and purity.
Product cooling to prevent degradation, particularly in heat sensitive compounds.
Jacket flow rate and temperature control to maximize heat transfer efficiency.
Condenser flow rate and temperature control.
High-quality components for minimal maintenance and long life.
Proper system layouts for optimal performance and ease of maintenance.
Benefits of Modular Wiped Film Evaporator Designs
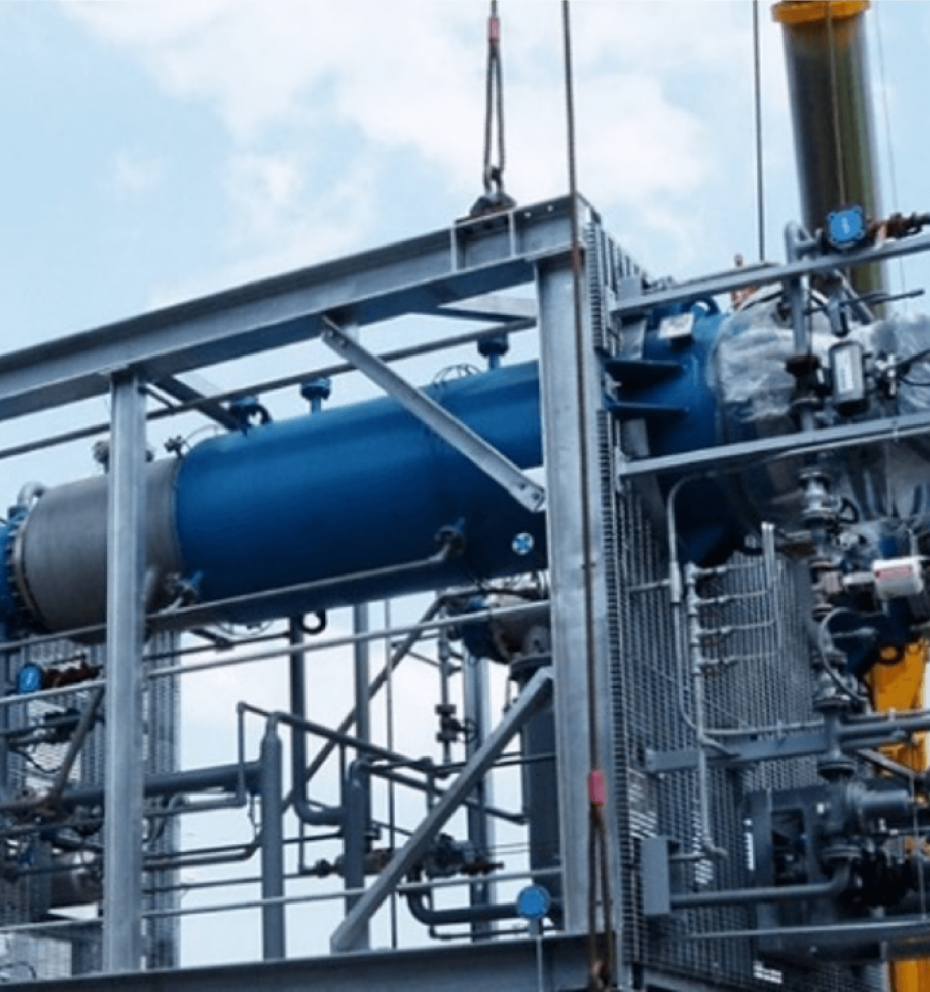
GMM Pfaudler provides Wiped Film Evaporator Systems as fully assembled process modules, delivering a range of key advantages that enhance both performance and efficiency, such as:
- Expertise in overall system design, ensuring optimal performance and functionality.
- Firm, fixed pricing to avoid costly project overruns.
- Single-source responsibility for seamless system integration and flawless project execution.
- High-quality shop construction for reliable and durable systems.
- Accelerated project timelines through efficient shop fabrication.
- Reduced total project costs through streamlined processes.
- Compact, space-saving design to optimize facility footprint.
- Minimized downtime of existing or adjacent site processes during new system installation.
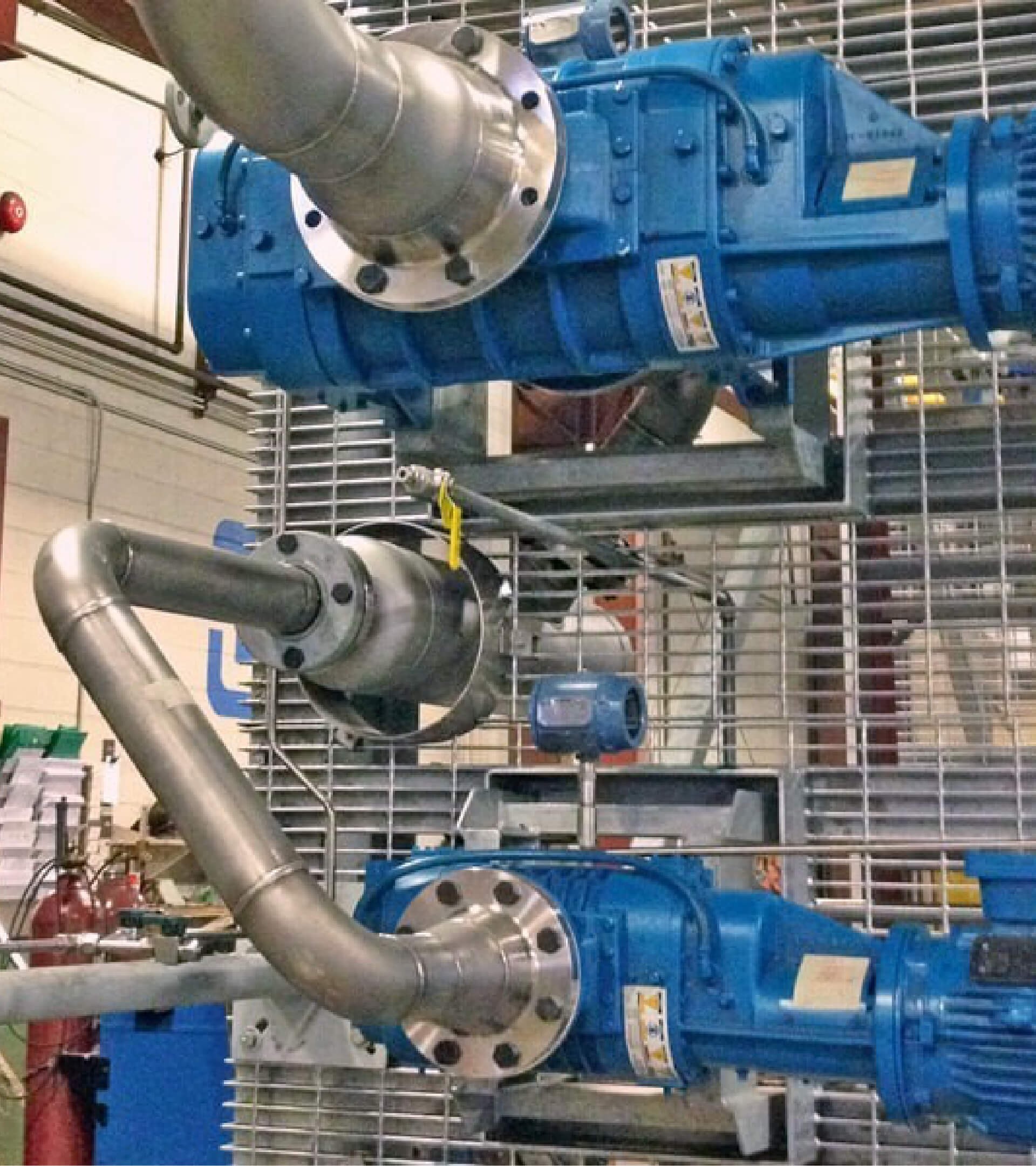
Vacuum System Design for Optimal WFE Performance
A reliable and consistent vacuum supply is essential for optimal performance in a Wiped Film Evaporator (WFE). WFE Systems typically operate under deep vacuum and several factors must be considered to ensure the right vacuum system is designed.
Importance of a Reliable Vacuum Supply
Without a stable vacuum, the evaporation process can be compromised, leading to lower efficiency, reduced throughput, lower purity and yield, and potential product degradation. Ensuring that the vacuum system is properly designed and integrated into the overall process is essential to achieve the best results.
GMM Pfaudler’s Expertise in Vacuum Technology
With our expertise in vacuum technology, GMM Pfaudler provides tailored solutions for WFE processes. We consider all factors to optimize performance and minimize maintenance. Our range of vacuum technologies ensures we can find the ideal match for your application.
Key Considerations for Vacuum System Selection
Several key factors must be considered when choosing the right vacuum system, such as:
- Proper staging with condensation handling
- Process stream physical properties
- Non-condensable loads
- Corrosion resistance
- Product melting points
- Potential for product polymerization
FAQ – Wiped Film Evaporator Systems
What is a Wiped Film Evaporator?
How do Thin Film Evaporators work?
Thin Film Evaporators, or Wiped Film Evaporators, use a rotating wiper system to create a thin liquid film on a heated surface. This thin film heats quickly and the large surface-area-to-volume ratio allows for efficient evaporation and prevents thermal decomposition and fouling. They are commonly used for sensitive materials in industries like fine chemicals, polymers, nutraceuticals, and pharmaceuticals.
What is the difference between a Wiped Film Evaporator and a Thin Film Evaporator?
A Wiped Film Evaporator is a specific type of Thin Film Evaporator. The Wiped Film Evaporator uses a wiper system to create and control a thin film for efficient evaporation, making it suitable for viscous and heat-sensitive materials.
What is the best evaporator for high viscosity applications?
Falling film evaporators are not suitable for high-viscosity applications, and distillation columns are similarly ineffective. Batch evaporation is highly inefficient due to low heat transfer coefficients, while using the production reactor for evaporation ties up the reactor and limits production capacity. Wiped Film Evaporators (WFE) are ideal for high-viscosity evaporation applications. The wipers in a WFE continuously move the viscous material down the wall, spreading it into a thin film, which significantly improves both the heat transfer coefficient and the evaporation rate.
Which evaporator system is best for fouling-prone applications?
Falling film evaporators, distillation columns, and circulated flash evaporators are not ideal for fouling-prone applications. These systems tend to foul easily, which reduces heat transfer efficiency and production capacity, and they require frequent cleaning shutdowns. Wiped Film Evaporators (WFE) are the best choice for such applications. The wipers in a WFE continuously clean the heat transfer surface while spreading the product into a thin film, ensuring high heat transfer rates and more efficient evaporation.
Which evaporator is recommended for heat-sensitive materials?
Distillation columns and batch evaporators are not ideal for heat-sensitive compounds because they expose materials to high temperatures for extended periods, leading to degradation and poor quality. Additionally, moving vapors between equipment causes pressure drops. Wiped Film Evaporators (WFE) are the best option for heat-sensitive materials. In a WFE, the residence time is only a few seconds, even in large systems, preventing degradation and preserving product quality. The internal condenser minimizes pressure drops and allows operation at low pressures, reducing the temperature required for evaporation.
What type of evaporator system is best for polymer processing?
In polymer processing, evaporation is commonly used for purification, such as the removal of residual solvents, monomers, dimers, or oligomers. Wiped Film Evaporators (WFE) are ideal for these applications. The wipers in a WFE spread the viscous material into a thin film, significantly improving heat transfer and increasing production capacity. Operating under high vacuum, the WFE also lowers the temperature, preventing degradation and maintaining product quality. In contrast, falling film evaporators, distillation columns, and batch evaporators are inefficient and unsuitable for high-viscosity polymer applications.
What type of evaporator is ideal for pre-polymer applications?
Wiped Film Evaporators (WFE) are ideal for separating isocyanates from pre-polymers. The short residence time and the ability to operate at extremely low pressures minimize the risk of thermal degradation while effectively reducing isocyanate concentrations to very low levels.
How to reduce volatile organic compounds (VOC) using an evaporator?
As environmental regulations for VOC content in polymers become stricter, evaporation plays a key role in reducing VOC levels. Wiped Film Evaporators (WFE) are ideal for this process. The wipers in a WFE spread the viscous material into a thin film, significantly enhancing heat transfer and increasing production capacity. Operating under high vacuum, WFEs lower the temperature required for evaporation, preventing degradation, and maintaining product quality. In contrast, falling film evaporators, distillation columns, and batch evaporators are ineffective for high-viscosity applications like VOC reduction.
How to purify Vitamin E (tocopherols) using an evaporator?
Many nutraceutical compounds, like Vitamin E (tocopherols), are heat-sensitive, making distillation columns and batch evaporation unsuitable due to prolonged exposure to high temperatures, which can cause product degradation and quality loss. Additionally, moving vapors between equipment causes significant pressure drops. Wiped Film Evaporators (WFE) are ideal for purifying heat-sensitive compounds. In a WFE, the process material's residence time is just a few seconds, even in larger systems, preventing degradation and preserving quality. The built-in condenser minimizes pressure drop and allows for low-temperature operation by reducing the pressure needed for vaporization.
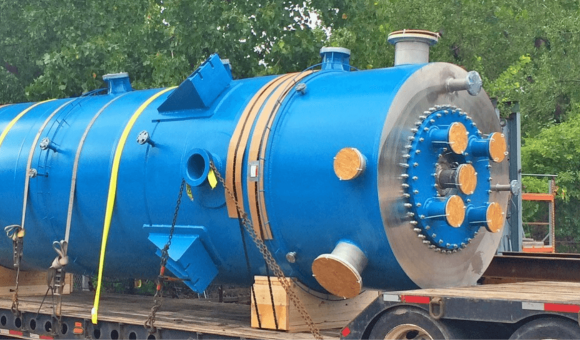
Equilloy Wiped Film Evaporator