Reaction Systems
Normag - Lab & Process Glass
Technologies
Overview
Glass reactors are the heart of any chemical laboratory or plant, where the following processes are held:
- Synthesis
- Extraction
- Distillation
- Concentration
- Emulsification, dispersion
They are mainly used in the pharmaceutical and chemical industry, but you can find them in food- and cosmetics laboratories and plants as well.
Design of the reaction system
A typical glass reactor is a glass vessel with a single jacket (for heat transfer fluid) or with a double jacket (with additional vacuum jacket for insulation). The Reactor is mounted on a support frame and is equipped with a glass lid. In addition to that, the reactor can also be equipped with:
- Bottom drain valve for media discharge
- Overhead stirrer with a stirrer shaft of a certain shape that fits the customer’s application
- Dropping funnel or dosing pump for adding liquids
- Condenser
- Reflux divider to either return condensate back to the vessel, or to distill it to another vessel (receiver)
- Dean-Stark assemble for azeotropic distillation
- Inline or Immersion Disperser
Main advantages of the glass reactors
- Perfect chemical resistance to almost all chemicals except for the concentrated alkaline solution and hydrogen fluoride
- Transparency which allows to monitor the process easily
- Standard jacketed reactor from Normag can stand temperature shock (dT) of 100K which is 2 times higher than most of the other glass equipment manufacturers
Double jacketed (with outer vacuum jacket) reactors are intended for the processes that are performed at +10oC or bellow. The outer vacuum jacket allows to:
- Almost 100% cooling efficiency generated by thermostat for cooling down the media, thanks to the vacuum jacket that is a perfect insulator
- Avoid frost formation on the surface of the vessel and therefore a complete monitoring of the process
It is extremely important to pay attention to the design of the bottom drain valve, because this is crucial for safe and continuous operation in a wide temperature range. Main advantages of the bottom drain valve that are manufactured by Normag are:
- The only materials that are in contact with the media are PTFE and glass
- Spring-loaded design eliminates the problem of difference in heat expansion coefficient of PTFE and glass and ensures safe operation in the whole temperature range without any risk of cracking
- 100% zero dead space design
- Full drain design guaranties that no media will remain the vessel after draining
Another important part of every unit that requires stirring is a stirrer guide and the type of the sealing in particular. For high-vacuum applications (down to 0.001mbar) magnetic couplings are recommended. For rough vacuum and slight overpressure standard single or double mechanical sealing are a good option. But for demanding process and especially for pharmaceutical applications we strongly recommend using our patented Interseal Lab 5000, which can be used in the temperature range of -20…+150oC at the sealing, under vacuum and slight overpressure, has a perfect chemical resistance (only PTFE and SiC are in contact with media) and does not create any flakes and so ensures a contamination free process.
Additionally, for process applications starting from 63l we can offer glass-lined vessels with a glass top (lid, condenser, dosing vessels, piping etc).
Picking up equipment that fits your application is not an easy task, especially if you have never done this in the past. We have many years of experience in engineering and supplying different reaction systems with different levels of automation. Feel free to get in touch with us, you will get full support in finding the solution that will 100% fit your application
Range of Products

Mixing Vessel 100-400L

Mixing Vessel Pilot 10-100L
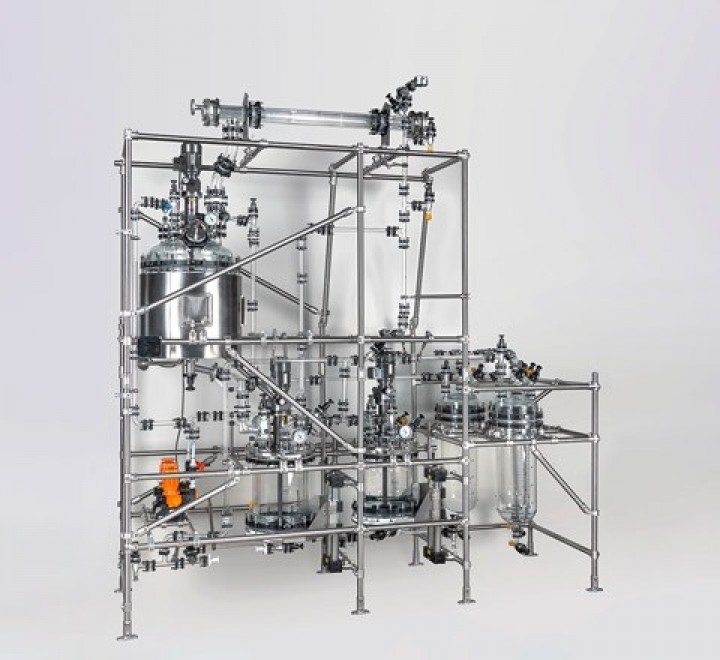
Reaction System above 100L
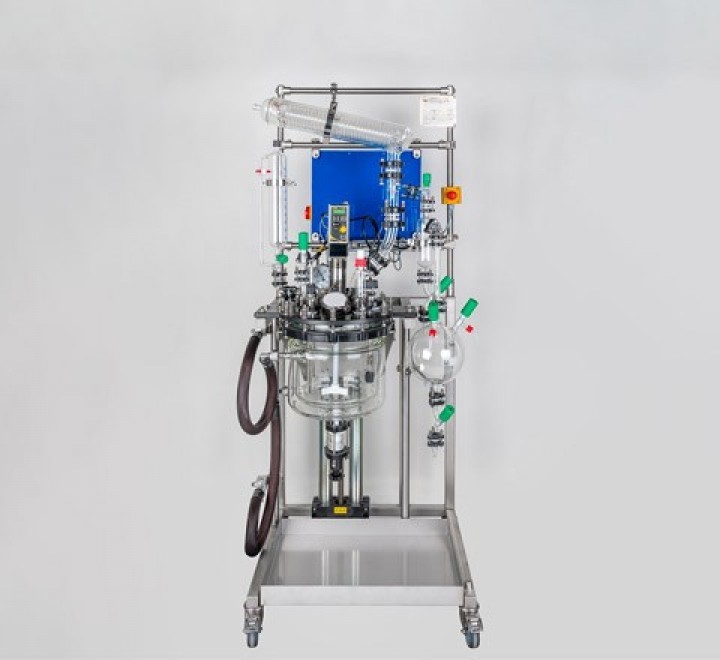
Reaction System LAB Max 5-15L

Reaction System Pilot 10-100L
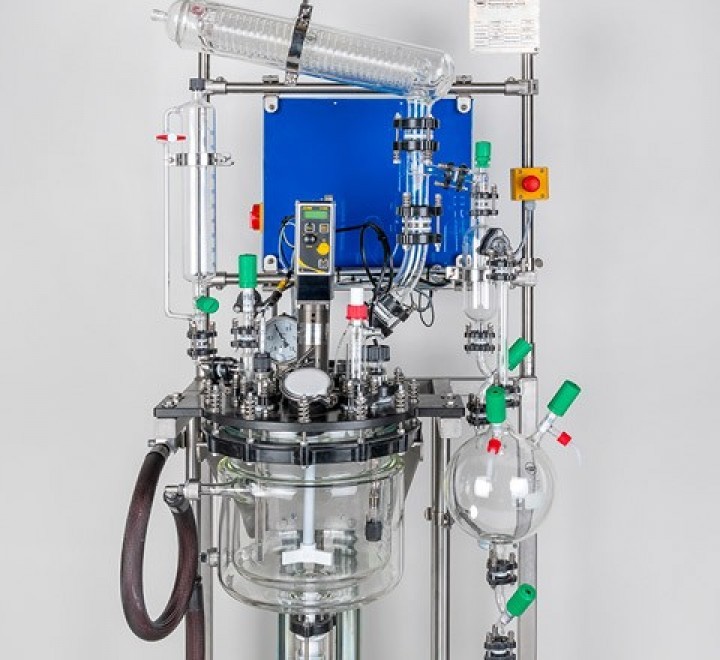