DIN Reactors
Pfaudler - Glass-Lined & Alloy Systems
Technologies
What is the DIN 28136 standard?
Before the DIN standard, every glass-lined reactor manufacturer had its own standards. Therefore, when a reactor was damaged, the user had to call the original manufacturer for repair or replacement. If processes based on glass-lined reactors are considered, downtimes can be hardly accepted. Likewise, depending on one supplier was barely accepted by the industry.
So, in order to increase the availability of reactors as well as components such as agitating systems, the industry and manufacturers worked out the DIN 28136 standard that defines a typical reactor, making the manufacturers of parts and components interchangeable.
Main Characteristics:
- Fixed design pressures and temperatures
- Fixed dimensions, H/D ratio of the glass-lined inner vessel: same nozzle table, nozzle orientation, diameters; allows to find on the market, at different manufacturers new or reglassed equipment suitable for replacing a damaged reactor
- Standardized manufacturing tolerances
- Standard agitator support flange: allows interchangeability of drive systems and sealing systems
- Standard agitator shaft head: allowing for interchangeability, modernization, retrofit of agitators, regardless of the original manufacturer allows modernization of the sealing system in relation to the modern INTERSEAL dry9000® system, regardless of the original agitator manufacturer
- Standard nozzle necks and flanges: allowing for interchangeability between manufacturer components, such as manhole covers, baffles, internals, gaskets, clamps, split flanges, and so on
In the frame of the mechanical standardization of the reactors, a standard for a minimum enamel quality of the so-called “chemical glass” was also defined: DIN EN ISO 28721-1 standard.

DIN EN ISO 28721-1: Minimum Requirements for Enamel
The DIN 28721 standard defines the quality requirements and acceptance conditions of vitreous enamel for glass-lined equipment in process plants:
- Glassing quality, visual aspects, glass thickness, thickness variation
- Checks, such as the spark test, thickness measurement, magnetic particle test (if necessary)
- Enamel defects, acceptable, not acceptable, repair methods
- Final quality report
- The above are the minimum requirements that Pfaudler meets and regularly exceeds in manufacturing.

DIN-AE Type Reactors
Characterized by a body flange: glass-lined reactor in two parts consisting of a base vessel and a cover;
- Defined in the DIN standard for sizes starting from 63 to 6,300 litres, but practically manufactured for up to 1,000 litres
- One-piece agitator
- In-line drive/ INTERSEAL sealing system.
The reactor must be two pieces, to allow accessing it for glassing procedures. Pfaudler recommends, as soon as a one-piece reactor is possible (from 1,000 litres or even below), to opt for a BE type reactor, which allows eliminating body flanges and the relevant disadvantages.

DIN-BE Type Reactors
- Characterized by a one-piece reactor where the largest opening is the manway (DN500 or DN600)
- Defined in the DIN standard for sizes starting from 1,600 to 40,000 litres and more, practically manufactured for up to 80,000 litres;
- Agitator introduced into the reactor body via the manway and assembled inside through Cry-Lock, Elco-Lock or CryCo-lock technology
- High flexibility and efficiency in agitation – many configurations available for agitation systems, for optimal adaptation to process requirements – as of today, agitation systems up to seven stages: achieved only by Pfaudler
- Very low downtime during maintenance, agitator replaced through the manway without having to dismantle any piping on the upper dish; shaft and drive remain in place when replacing a turbine
- In-line drive/ modern INTERSEAL sealing system or traditional mechanical shaft sealing unit with lube system
The DIN-BE type reactor is the most used worldwide for its benefits:
- Higher vessel resistance to pressure
- Reduced leakage rates – largest gasket is the manhole gasket
- Easy to clean, due to reduced number of gaskets and reduced gasket length
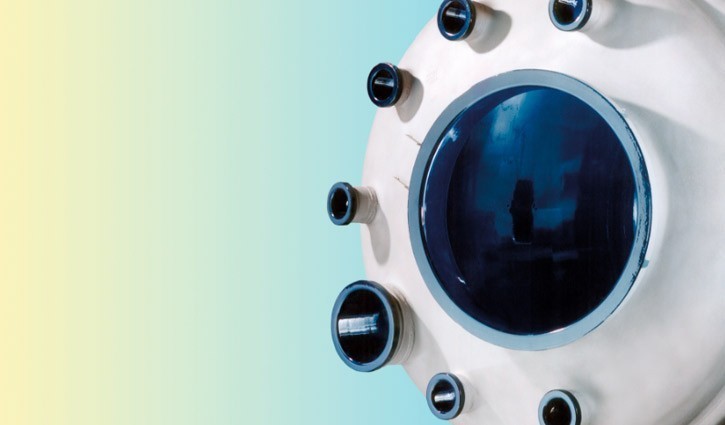
DIN-CE Type Reactors
- Characterized by a main opening on the top dish for mounting the agitator; DN up to 1350 mm
- Defined in the DIN standard for sizes starting from 1.,600 litres up to 40,000 litres
- Agitator fit in the reactor body via the main opening on the top dish; built-on process piping must be dismantled from the top dish, in order to remove/ replace an agitator
- Low flexibility in agitator shapes – multi-stage almost impossible;
- In-line drive/ INTERSEAL sealing system or traditional mechanical shaft sealing unit with lube system
DIN-CE reactors were designs before the DIN-BE versions, for volumes above 1,000 litres. Once agitator solutions, such as the Cryo-Lock technology were available, when it was possible to introduce the agitator through the manhole and assemble it inside the reactor, the DIN-CE reactor configuration became obsolete.
Today, existing DIN-CE reactors still in operation are frequently retrofitted with Cryo-Lock agitators, in order to benefit of the advantages of this technology for process efficiency and reduced downtime during maintenance.